The director of a lumber core manufacturing plant was in his office when he suddenly heard an explosion-like sound coming from the Boiler Room in the production area. As he went to the dust collector to stop the operations, he saw Boiler 1 had severely deformed and some material nearby was on fire. He gathered his workers to fight the fire using the premises water hydrant. The firefighters arrived 1 hour later and helped to extinguish the fire. 7 hours later, the fire was completely extinguished. Due to the incident, 2 of the boiler helpers were injured.
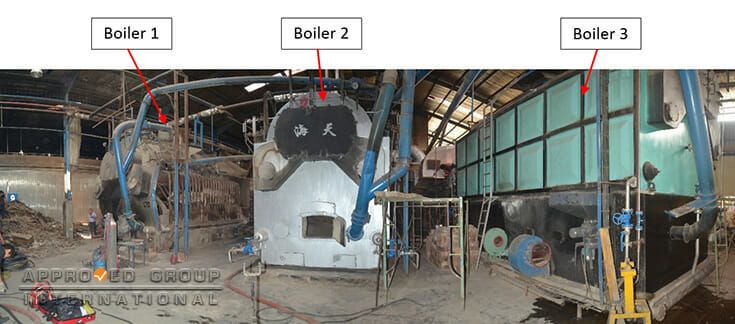
The construction features of these boilers are a combination of water tubes and fire tubes. There are two (2) layers of water tubes connected to each side of the boiler drum; twenty-five (25) tubes on the upper layer (UL) and another twenty-five (25) tubes on the lower layer (LL). The water is first pumped from the water tank to the raw water tank inside the boiler room. The water is heated simultaneously through two (2) methods of heating:
- Fire from the combustion chamber located underneath the water drum.
- Flue gas flowing inside the fire tubes located inside the water drum.
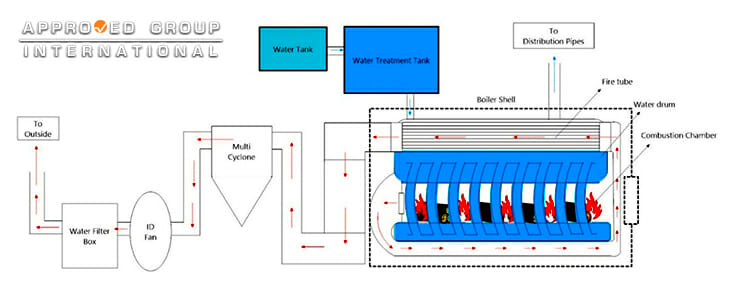
Only Boiler 1 was severely damaged and no signs of damage were observed on the other2 boilers. Bulging was observed at the lower front section of Boiler 1. The firebricks from the combustion chamber were observed to have collapsed mainly at the front section. Watermarks were also observed on the lower exterior surface (fire side) of the water drum.
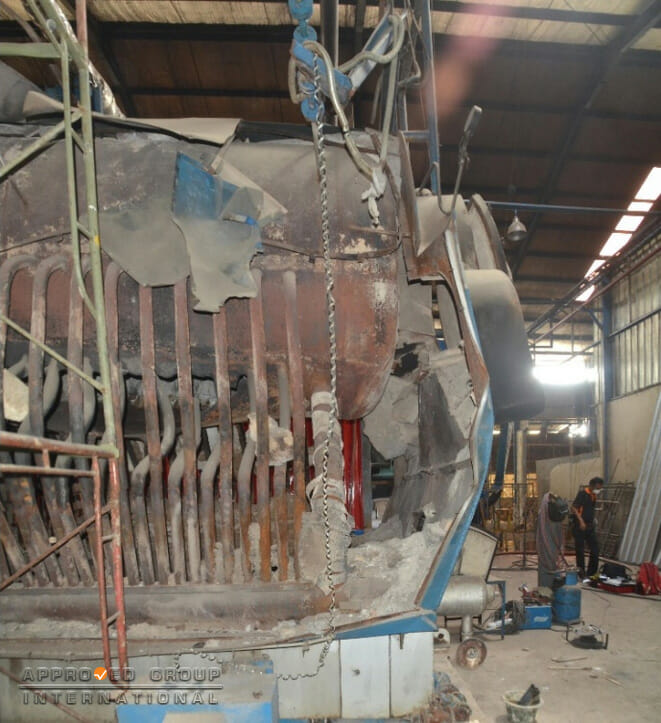
This indicates that the explosion was within Boiler 1 at the lower section of the boiler and due to this, the shell plate and insulation materials were damaged and thereby exposing the interior section of the boiler. Multiple isolated cavities/ porosities were observed at the weldment joints between water tubes and boiler drum shell on the right section as well as in the left section. The pitted surfaces were observed at the ruptured section of water tubes as well as adjacent unaffected section of water tubes. Thinning of the water tubes mouth adjacent to the welded joint was also observed.
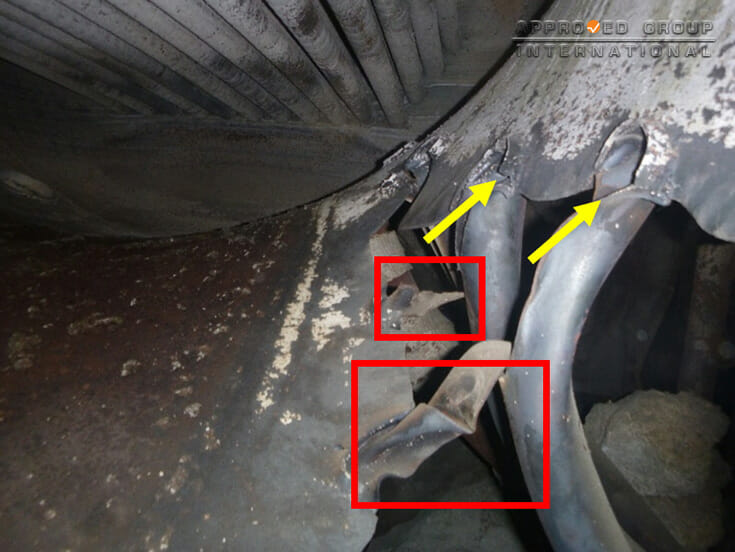
Cavities were also observed on the welds located along the ruptured section of the water drum. Localized corrosion was also observed at the heat-affected zone (HAZ) of the welding joints and inside the water tubes connections.
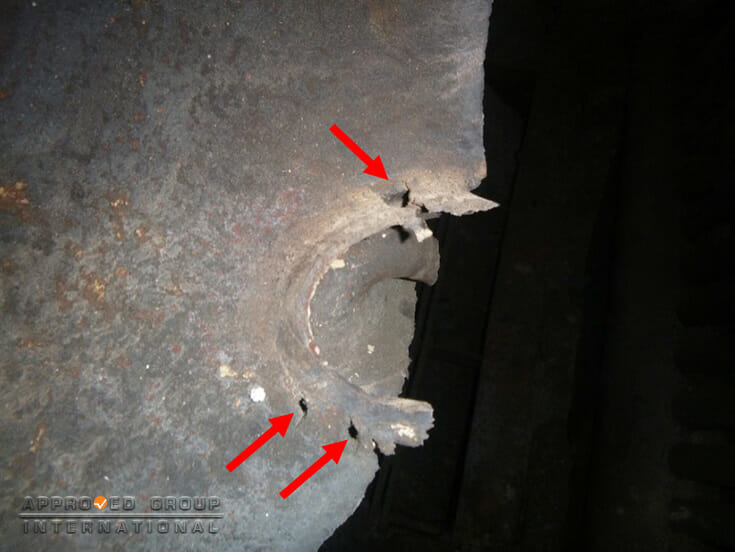
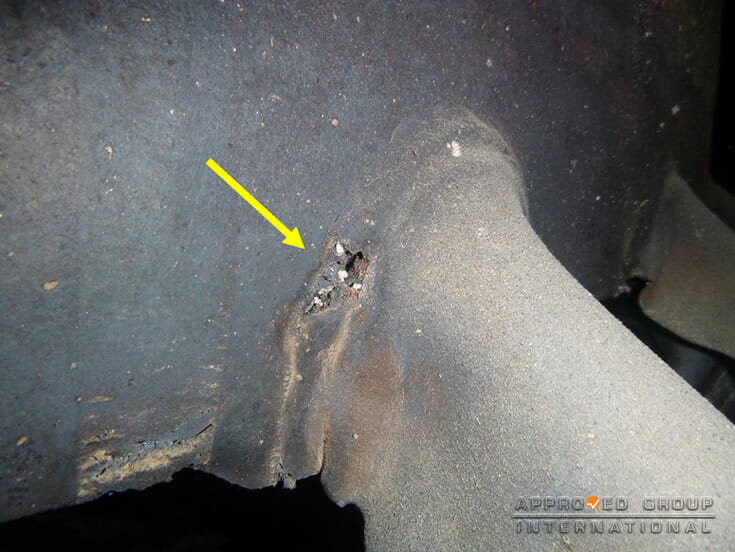
Based on the Team’s findings, the boiler drum rupture which then leads to subsequent explosion and fire can be illustrated as follows:
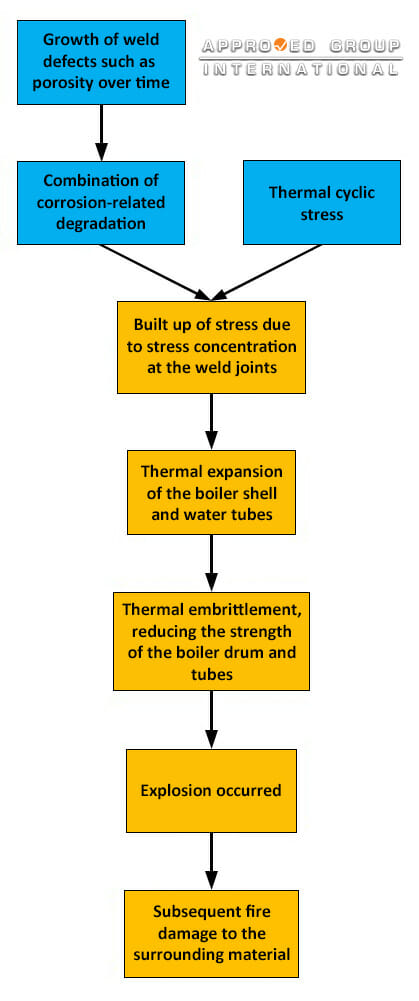
Based on the on-site investigation, inspection and examination, damage analysis and interpretation and elimination of probable causes, the Team found that the cause of explosion was due to the failure of the internal components of the boiler, caused by the propagation and growth of inherent weld defects in combination with corrosion-related degradation and cyclic thermal stress.