An air handling unit (hereinafter referred to as AHU) room is normally equipped with a gaseous fire suppression system which utilised INERGEN, which is a mixture of nitrogen, argon and carbon dioxide gases, stored gas cylinders.
The system is also composed of mainly smoke detectors, discharge nozzles and control panels. Displayed below, the basic arrangement of the gaseous fire suppression system.
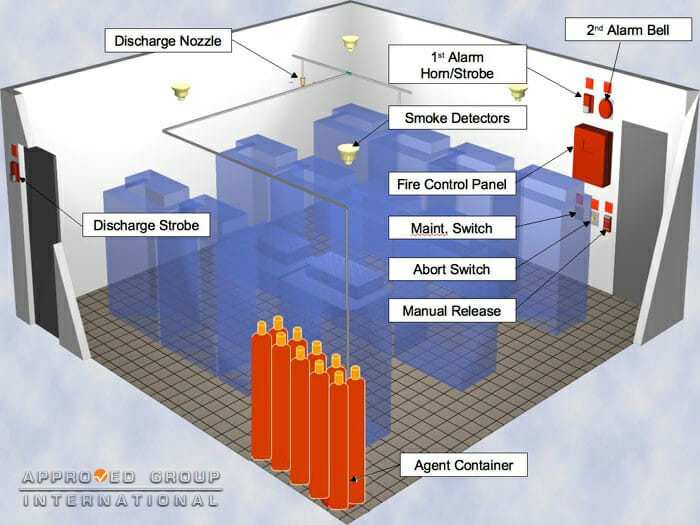
An explosion was reported to have occurred within the premises of a publication company. The Assistant Manager, was in the office when he heard the explosion. He then proceeded to level 1 and found that the explosion had occurred within the AHU L1.02 room. The AHU room was mainly equipped with the AHU and the gaseous fire suppression system. There were eighteen (18) units of INERGEN gas cylinder of the gaseous fire suppression system.
The team found only one (1) INERGEN gas cylinder unit was damaged in the incident (refer to Photograph 1).
Tear damage was observed from the middle downward of the INERGEN gas cylinder’s body (refer to Photograph 8 of Appendix 1).
The torn body was found opened outward with irregular jagged pattern. The upper section of the torn body and the lower section of the torn body revealed shearing characteristic. The shearing indicates the area which had failed last due to the explosion.
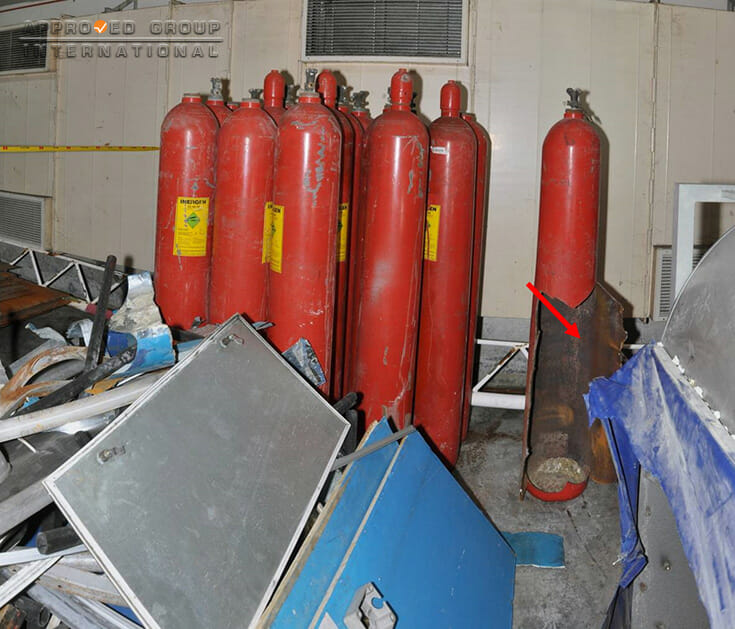
Further examination on the internal surface of the failed INERGEN gas cylinder revealed pitting along the fractured surface (refer to Photograph 2).
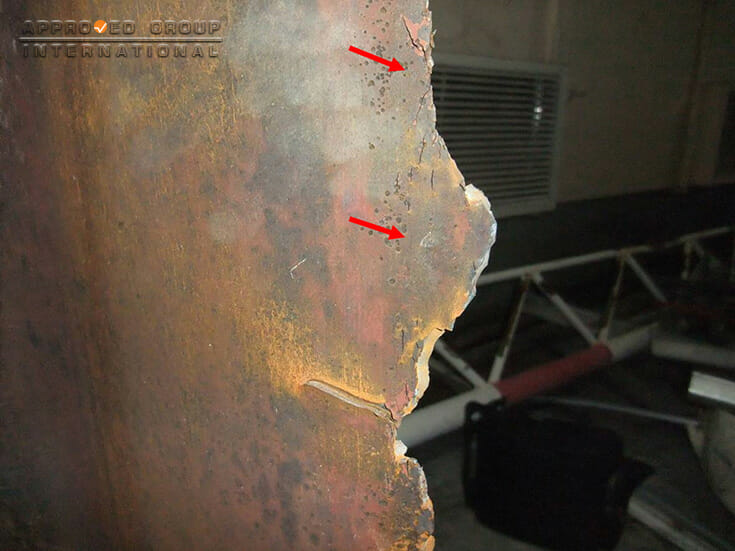
No discolouration or heat damage was observed on the outer colour of the affected INERGEN gas cylinder. Cross section of the fractured surface revealed brittle characteristic on the surface towards the inner surface and sheared characteristic towards the outer surface (refer to Photograph 3).
These characteristics indicate that the failure originated from within the INERGEN gas cylinder.
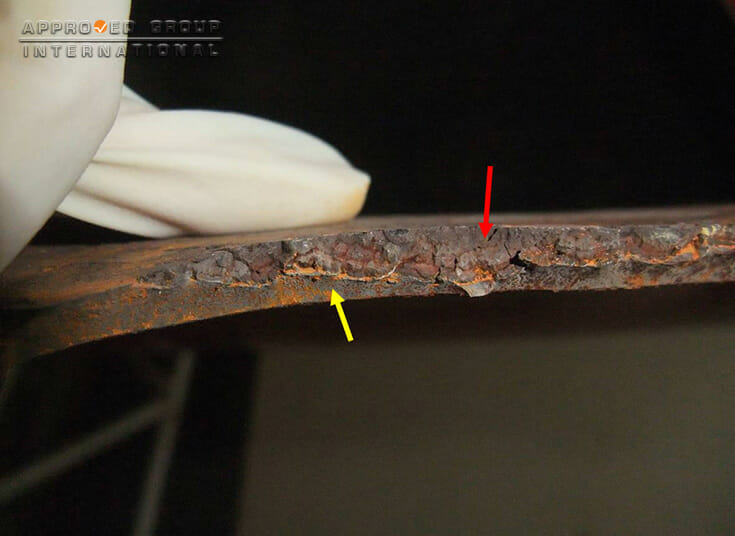
Corrosion is the degradation of a material due to a reaction with its environment. There are several types of corrosion which include:
Aqueous corrosion | Atmospheric corrosion |
Galvanic corrosion | Stray-current corrosion |
Molten salt corrosion | Liquid metal corrosion |
High-temperature gaseous corrosion | Crevice corrosion |
Filiform corrosion | Pitting corrosion |
Pitting corrosion is characterized by sharply defined cavities which can cause failure by perforation while producing only small weight loss on the metal.
An examination on the failed INERGEN gas cylinder revealed signs of oxidation within the inner surface. A closer examination revealed the formation of pits along and adjacent to the fractured surface.
Pitting occurs when one (1) area of a metal surface become anodic with respect to the rest of the surface. There are several causes of pitting corrosion which include:
- Local inhomogeneity on the metal surface
- Local loss of passivity
- Mechanical or chemical rupture of a protective oxide coating
- Discontinuity of organic coating
- Galvanic corrosion from a relatively distant cathode
- Formation of a metal ion or oxygen concentration cell under a solid deposit
Stress-corrosion cracking (hereinafter referred as SCC) is a cracking phenomenon that occurs in susceptible alloy and is caused by the conjoint action of tensile stress and the presence of a specific corrosive environment. SCC occur under three (3) conditions:
- Specific crack-promoting environment
- Metallurgy of material must be susceptible to SCC
- Tensile stresses must be above some threshold value.
Further examination on the pitting revealed the formation of crack transversing along the diameter of the pit (refer to Photograph 4).
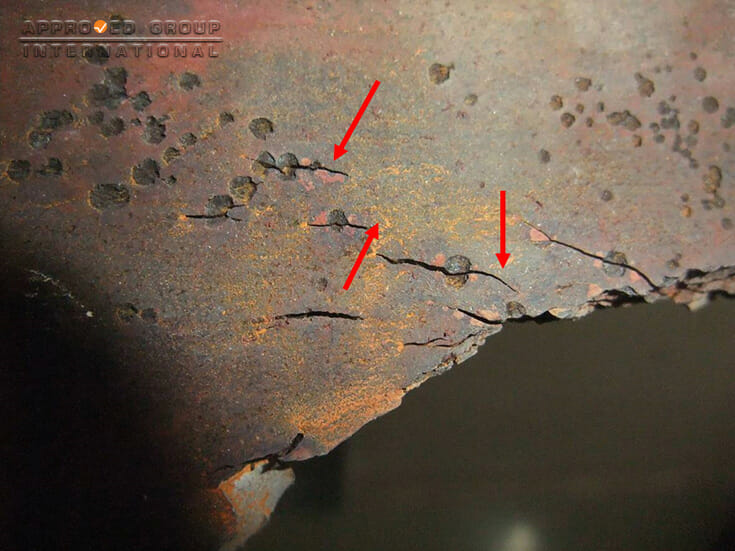
ASM international state that under the ‘corrosion tunnel model’, tunnels of corrosion are formed at the crack tip until the ligaments fractured in a ductile manner. The crack thus propagated by alternating corrosion and ductile rupture.
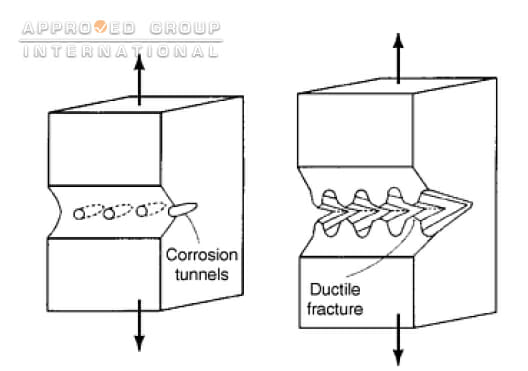
The formation of the pitting corrosion on the inner surface of the INERGEN gas cylinder created a susceptible area for crack. Under the stress of the INERGEN gas pressure, the metal surface was constantly under stress which promoted the propagation of the crack.
The crack propagation continued to the extent that the gas cylinder could not further contained the pressure of the INERGEN gas thus causing the rupture of the INERGEN gas cylinder and causing the explosion.
Based on the damage analysis, witness accounts, the process of elimination, as well as physical evidence found on-site, the explosion was found to have originated from corrosion of the inner surface of the INERGEN gas cylinder.