At approximately 1620 hours on Sunday, 15 December 2019, the shift leader at a boiler system company heard a loud noise coming from the outside area of the premises. He rushed out and saw that the chimney had collapsed. Acting quick, he alerted the production team and shut down the boiler operation. There was heavy rain and a windstorm going on at the time of the incident.
AGI was appointed to investigate the cause for the chimney’s collapse. Although circumstantial evidence pointed to the windstorm as the cause of damage, further examination by our team proved this was not the case.
The investigation process kicked off with a site visit to inspect the location of the incident. During the inspection, we conducted interviews with the eyewitness, gathered information, recorded statements, 3D scanned and made a sketch layout to document the scene.
The chimney’s structural details were recorded and thoroughly inspected. It was found that the company operates 24 hours daily and the boilers are only shutdown for an inspection by the Department of Occupational Safety and Health (DOSH) once every fifteen months. During this time, equipment maintenance is also conducted.
Considering the inspection was conducted two weeks after the incident, the chimney had already been cannibalised and cleared away from the site by then. Hence, it is a possibility that some crucial evidence may have been disturbed prior to our inspection. The premises did not show any signs of widespread damage from the windstorm and apart from the collapse of the chimney, other sections remained clear. The cannibalised chimney was examined and some dents, deformations and material tears were recorded. General corrosion was seen on the interior and exterior surface of the deformation area. Observations suggested that the initial collapse started at the chimney’s cross-sectional area after the first flange joint, about seventeen meters from the ground.
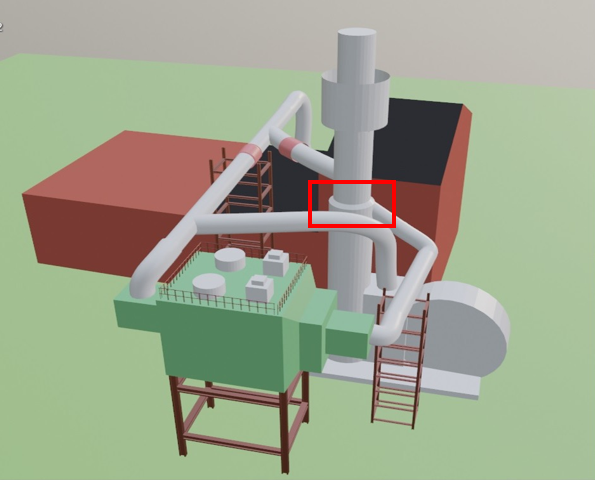
A few possible causes for the collapse were identified, namely:
Collapse due to external impact – if there were any heavy machinery being operated near the chimney, this could destabilise its structural integrity and cause damage. However, there was no impact damage on the chimney base and no heavy machinery activities were being carried out at the time of the incident thus ruling out this possibility.
Collapse due to wind storm – the hourly wind and rainfall data for 15 December 2019 were retrieved and interpreted using the Enhanced Fujita Scale. In the vicinity of the premises, there was no uprooted trees or damaged structural ridges observed. The analysis revealed that both the wind speed and rain fall during the time of incident would not have been able to cause any structural damage to the chimney concluding that this was not the cause of the collapse.
Collapse due to poor design – with the external factors showing up inconclusive, we then began to look at the chimney itself to identify the cause of collapse. The chimney’s general arrangement drawings did not contain any consultant approval, however there were two holes cut on its second section to accommodate horizontal flue ducts (HFDs) 1 and 4 from the boiler and electrostatic precipitator (ESP). As the cut was made at its shell, this would have compromised the chimney’s structural integrity. Taking the multiple flue duct entry into consideration, this would cause different temperatures to rise along the inner wall of the chimney which is compressive on the hot face and tensile on the cold face. Adding in the chimney’s dead load, it could cause tensile stress which may deform its structural integrity. However, atmospheric moisture could only seep in if the operational and maintenance activity of the chimney was compromised. As such, the collapse was not due to design error.
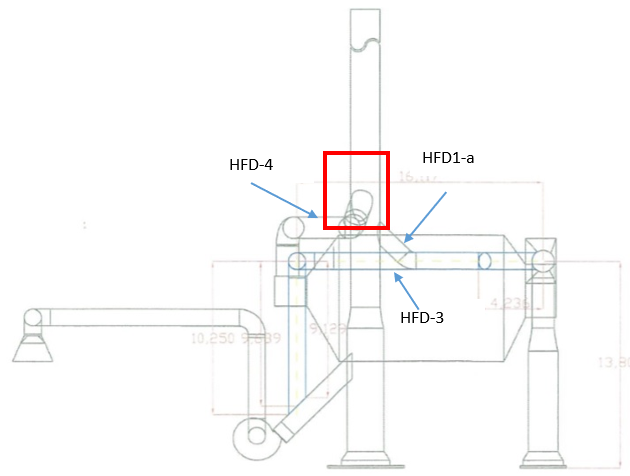
Collapse due to lack of maintenance – The chimney’s condition largely depends on the regular maintenance of the ESP and HFD’s as there should be zero tolerance of moisture into these parts. If moisture ingression occurred to the ESP and HFD, this would result in severe corrosion and failure of the chimney’s structural integrity. When inspected, there appeared to be several maintenance issues observed by the team. The HV transformer of the ESP showed signs of oil leak and the discolouration indicated that there was no oil replacement or filtration done during the maintenance schedule. The silica gel inside the breather of the transformer indicated moisture ingress into the transformer oil tank. The access door key of the rectifier cubicle was broken proving that no maintenance could have been carried out there.
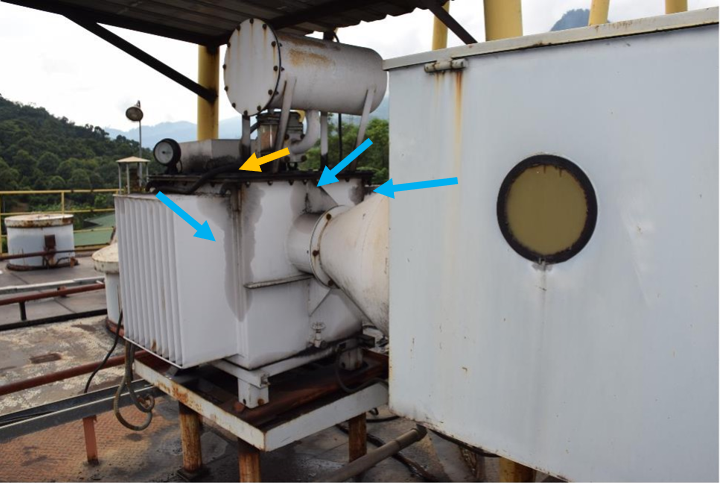
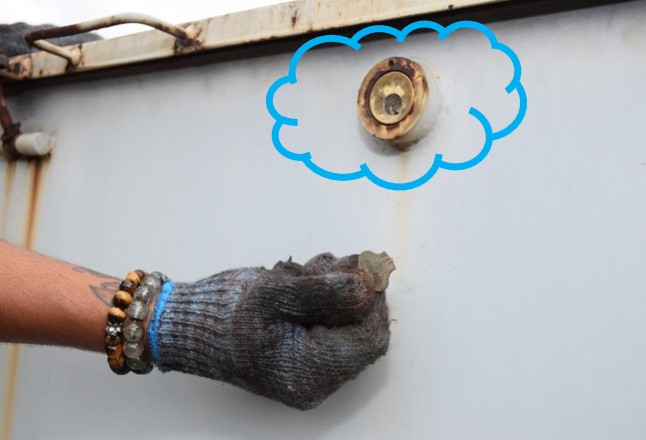
The other levels also showed signs of poor to no maintenance including severe corrosion, material loss, dislodgement of several discharge electrodes and more. There were also layers of oxides found formed on the inner walls of the HFD whereas severe corrosion on the D2 flaps had accumulated as a result of negligence over the years. The ESP is an environmental protection equipment which filters out the air pollution causing particulates from the flue gasses emitted out of the boiler. The ESP collects the suspended particulates in the flue gas through ionization method. When the ESP is in a decommissioned condition, it is not able to filter out the suspended pollution causing particulates from the flue gas. The state of the ESP also causes a disruption in flue gas flow. This disruption flow due time accumulates the suspended particulates in solid form at the ducting before the ESP.
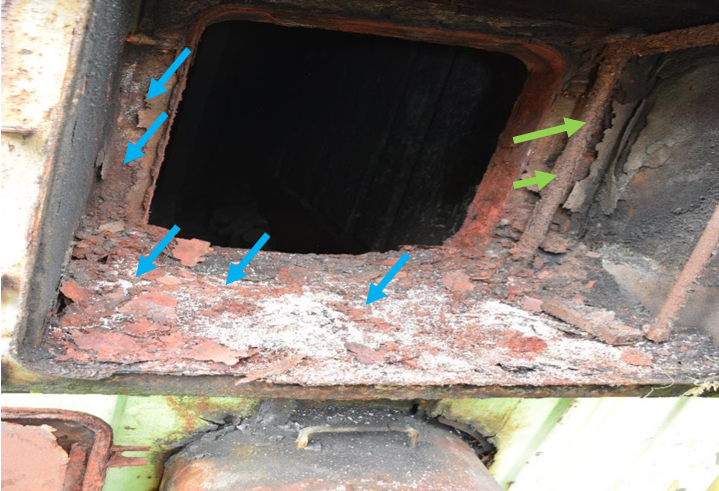
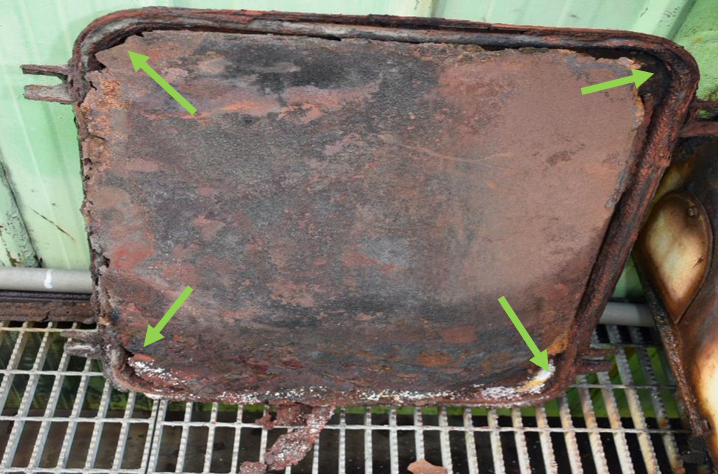
In any condition, if moisture entered into the HFD1, the hot flue gases would increase the weight of the particulates suspended along the gas entrain tremendously. This would condense the suspended particulates and over time will form as a layer. These layers then form a carbon damp inside the HFD1 significantly increasing its total dead weight beyond the designed dead load capacity of the chimney. Our investigation found that although the maintenance team had tried to seal an airgap found at the flange with a silicone sealant, they did not achieve the desired result. Therefore, the accumulation of carbon damp residuals due to ESP’s unavailability and the seeping of moisture contributing to further aggravate the condition had increased the dead weight of the chimney structure. The condition destabilised the entire chimney and HFD’s arrangements causing both to collapse. The cause of collapse was found to be due to lack of maintenance.
Often when any piece of equipment or machinery fail, it can be tricky to identify the cause of the accident as these are complex systems. This could also prove to be a challenged later on during the insurance claim process. However, with the right team of experts, analysing incidents such as this and getting to the root cause of it undoubtedly gets much easier.
Interested in getting our help for a similar situation? Get in touch with our team of professionals today