A Second Stage Compressor (SSC) failed at an air collection company. Prior to the incident, a power failure occurred on the same day at 1700 hours which caused the Main Air Compressor (MAC), which houses the SSC, to trip. The power failure was rectified at 1900 hours and the plant process was restarted thereafter. The MAC was the first equipment to be restarted which later gave out an abnormal high reading of vibration from the SSC. The high vibration subsequently caused the interlock system of the MAC to trip the MAC. Personnel of the air collection company later dismantled the SSC and found that the balancing pin of the impeller of the SSC had dislodged from its original position.
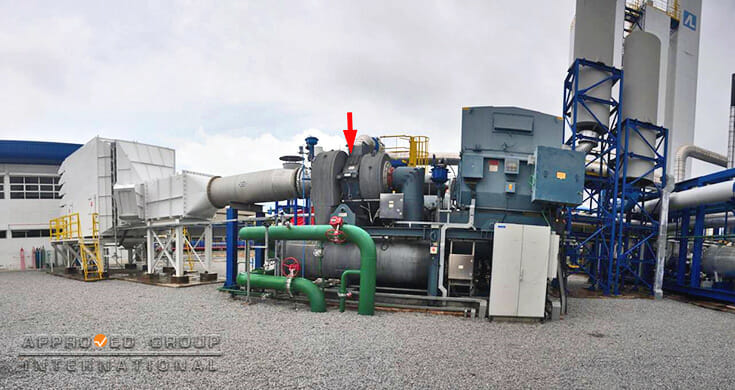
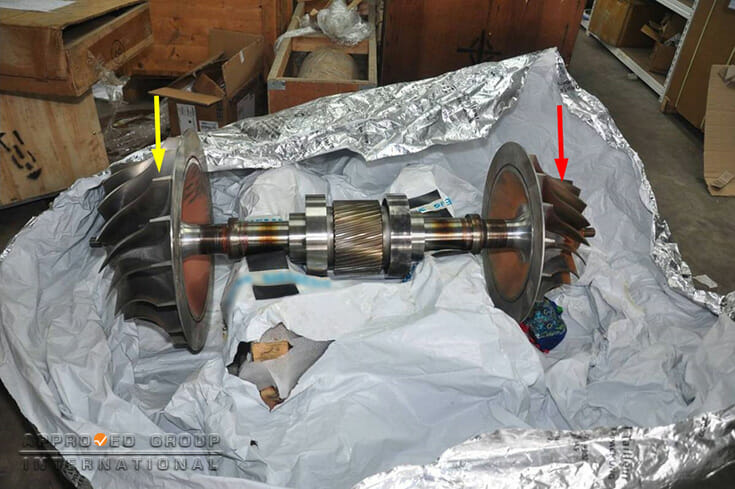
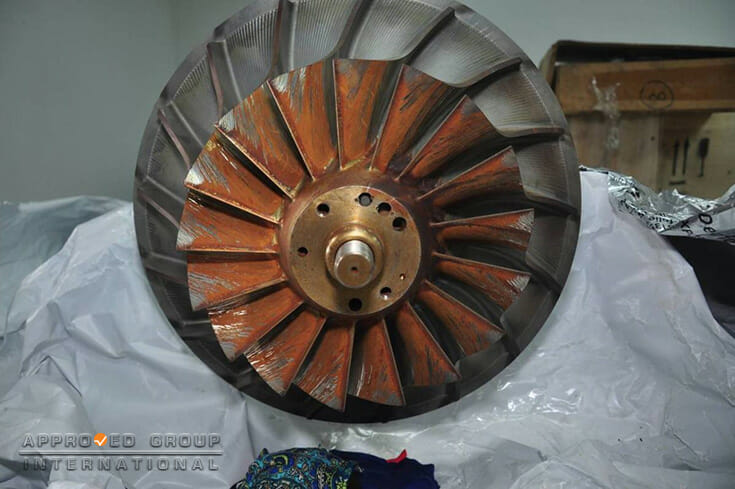
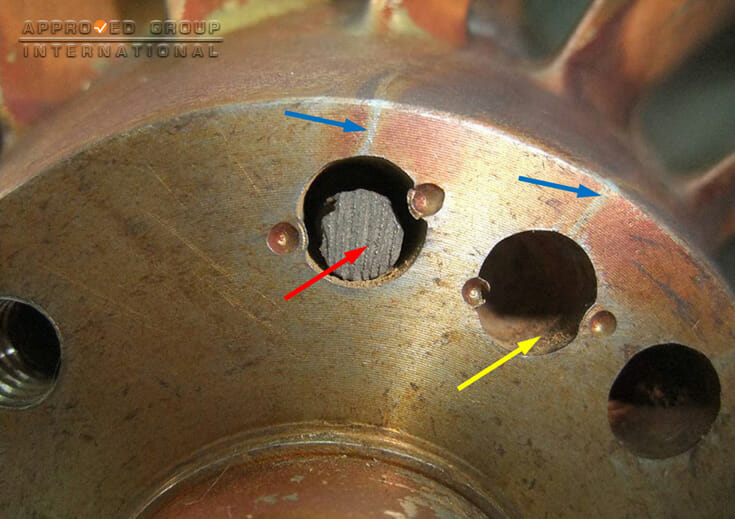
The failed balancing pin was further tested under SEM for corrosion. Corrosion is defined as the degradation of a structural material by chemical reactions with the environment which usually by the process of oxidation. The SEM analysis revealed a microstructure consisting of tungsten beads with large voids in between and traces of iron and nickel. This porosity was observed towards the perimeter of the failed balancing pin. Displayed below is the microstructure of the failed balancing pin under SEM.
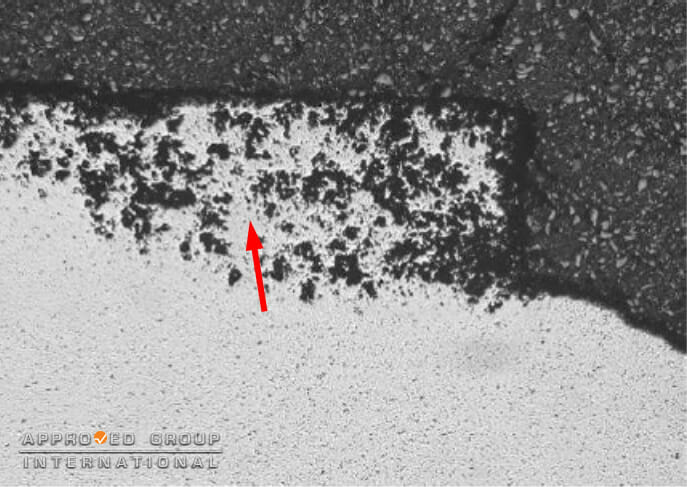
The finding indicates that a selective corrosion which attacked the binding phase, iron-nickel, had occurred on the outer surface of the failed balancing pin.