An explosion of an induction furnace at a spare parts manufacturing plant damaged the furnace and caused the molten metal to spew around the area. The 4-year-old furnace was a 750kW medium-frequency coreless induction furnace with a capacity of 1 tonne. The melting of the scrap metals takes about 4 hours at 1500°C. The furnace is mounted on high-intensity steel frame and support. It is fitted with hydraulic control system for tilting and consists of a crucible surrounded by hollow copper induction coil which encircles a layer of refractory lining surrounding the interior circumference. The induction coils receive alternating electric current from an induction power unit to generate an electromagnetic field which penetrates through the lining layer and couples with the conductive metal charge (scrap metal) within the furnace crucible. This induces secondary eddy current in the scrap metal and converts the electric energy to heat without any physical interaction between the induction coil and the work piece. The eddy current heats the metal charge to its melting point and set-up electromagnetic forces which produce stirring action, resulting in both homogenisation of the chemical composition and assimilation of any bath additions. To prevent overheating and potential failure, the induction coil is cooled by water circulating through the hollow tubing. Figure 1 is the basic diagram of the induction furnace.
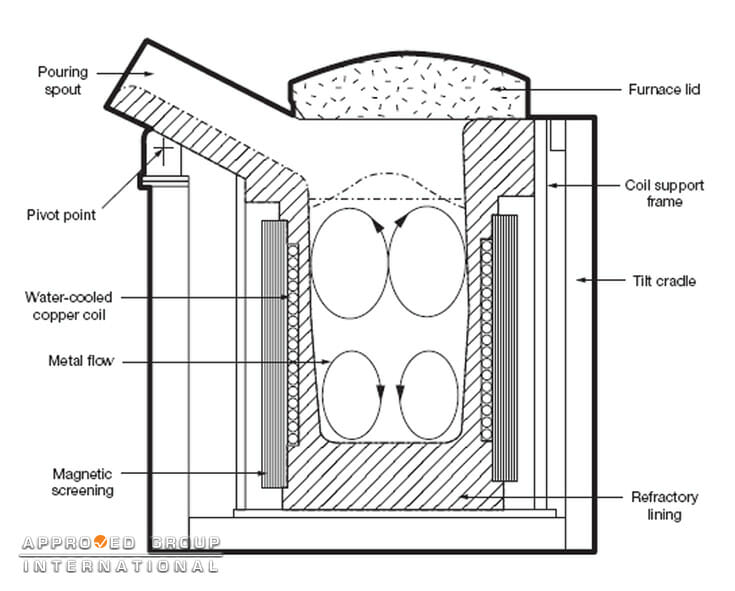
Approved Forensics Sdn Bhd (AFSB) was appointed to investigate the cause of the failure of the furnace. The Team found that the crucible former was removed and the water hoses had been disconnected.
Cracks and damage were observed on the upper surface of the refractory block at the 2 o’clock to 4 o’clock positions. Severe localised damage was also found on the mid-lower section of the furnace from 1 o’clock to 2 o’clock positions.
The refractory lining of the crucible and refractory layer between turns of the coils were destroyed, causing the leakage of the molten metal out of the furnace. The induction coil from turn-14 to turn-18 was welded with solidified molten metal.
The most damaged coils were found to be turn-14 and turn-15, where severe inward deformation and damage were observed. A punctured hole was also observed on turn-14.
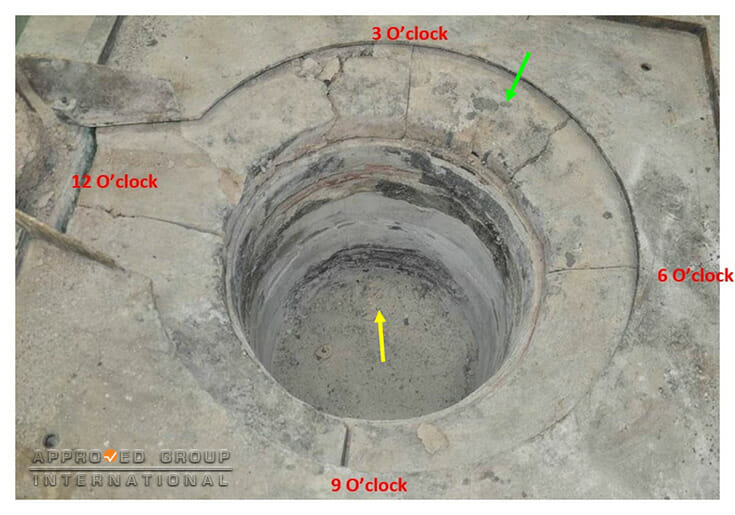
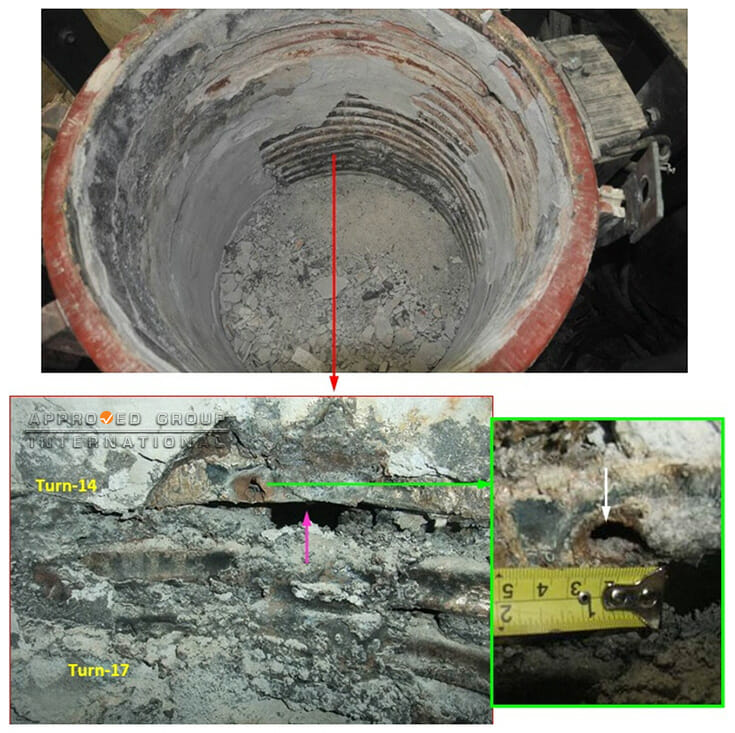
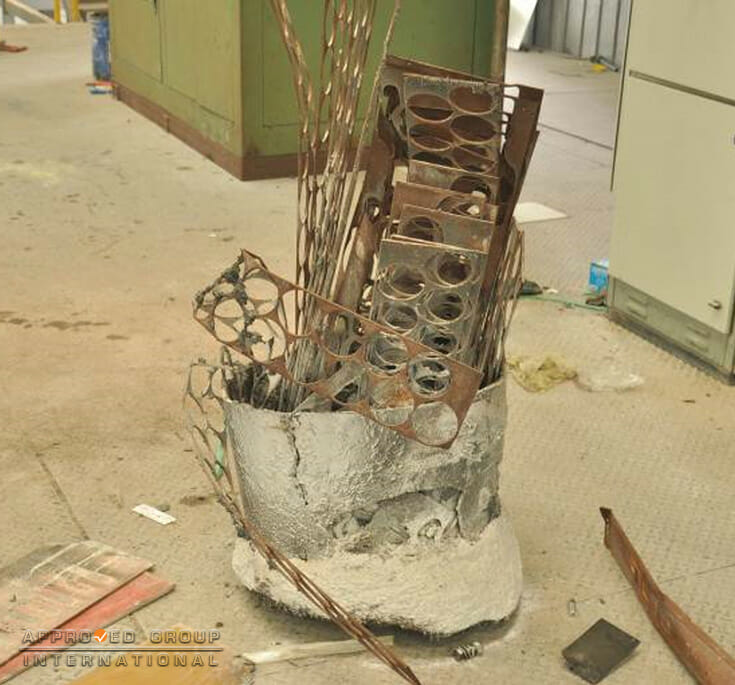
The explosion was due to a bridging that occurred in the furnace. Bridging exists when the metal charge fails to make contact with the molten metal in the furnace crucible. Cooler metal charge was added to regulate the temperature of the molten inside the furnace. During the melting cycles, crust of slag, which contains impurities and air or vapours, formed across the top of the molten metal to become a bridge layer, which occurred when the metal charge failed to penetrate the bridge layer, thus prevented it from moderating the temperature of the molten metal during the melting cycle. This caused the molten metal below to superheat. Further examination revealed that the lower section of the removed crucible former was severely cracked and broken, and this is the level where the molten metal is separated from the metal charge. This further suggests that the explosion occurred at the area between the molten metal and metal charge, where bridging had occurred. The superheated molten metal eroded and failed the refractory lining, allowing the molten metal to melt through the induction coils. This caused the water to leak out and come into contact with the hot molten, instantaneously evaporating water to become steam, which resulting in an explosion, creating a blast force that had sufficient energy to push and spew the molten metal out of the furnace crucible.